Get Your Event Chains
Fully Defined
Clarify the event chain requirements for your complex, dynamic architecture automotive projects. Manage complexity effectively and reduce project risks.
For OEMs and Tier 1 suppliers.
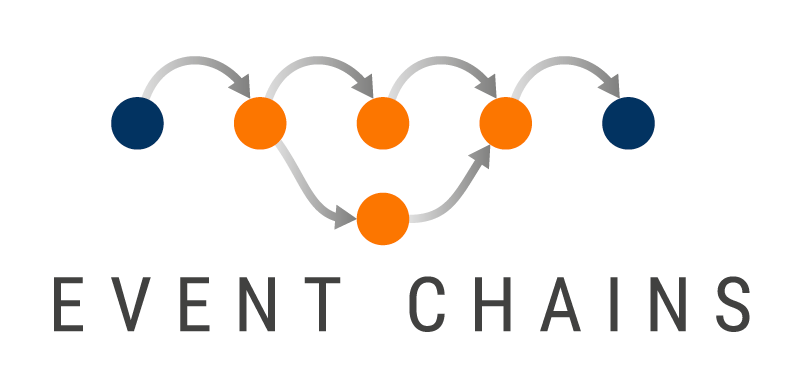
Get Your Event Chains
Fully Defined
We would be happy to send you further information.
Event Chain Engineering
By using model-based simulation for complex, dynamic architecture automotive projects, this INCHRON service delivers a comprehensive overview of your project’s key event chains and their influence on each other under all operating conditions.
Recognizing the challenges OEMs and Tier 1 suppliers face as they move to new E/E architectures, it pinpoints the issues caused by sharing common resources across different functions.
Teams using this service can make better architecture decisions thanks to “What if?” analysis, boosting project efficiency through interdisciplinary collaboration. The service can also be seamlessly integrated into ongoing projects.
USE CASE
Event Chains for OEMs
USE CASE
Event Chains for Tier 1s
USE CASE
ECU Performance Analysis
USE CASE
Including Timing in Requirements Documents
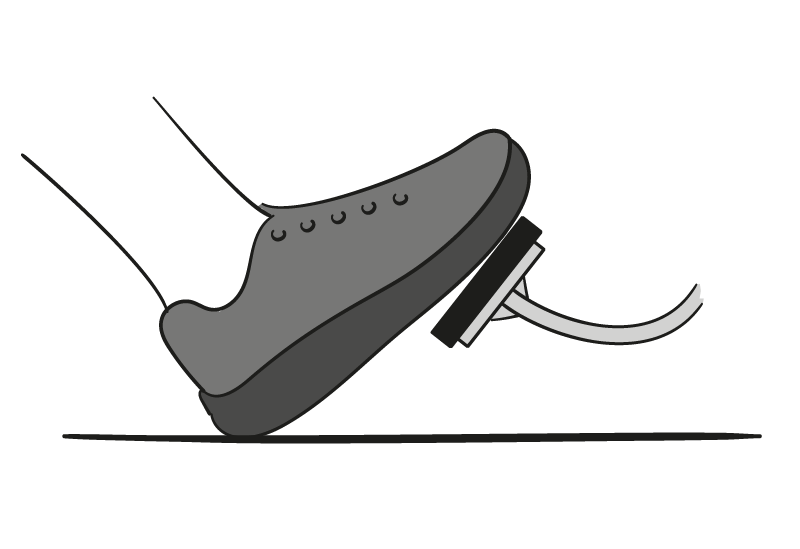
Event Chains for OEMs
Focusing purely on functionality in requirements documents leaves a lot open to interpretation, especially regarding timing. For example, how much time is there for object detection, decision-making, and brake application in an emergency braking system?
By starting with an end-to-end timing requirement for this chain of events, it becomes clear to all involved what the total available time is for the task. As the project develops, this can be refined, with timing defined for each step in the application’s process.
Event Chains for Tier 1s
Without clarity around the time available to execute functions and tasks, it’s challenging to determine who in a project is responsible for any functional issues that arise.
Demanding timing requirements alongside functional requirements from OEMs makes it easier to determine the cause of software-related issues when communicating with other suppliers working on a project.
USE CASE: ECU Performance Monitoring
How much more functionality can your automotive ECU support? What impact would moving code from one core to another have? And has your latest code release introduced potential corner-case failures?
INCHRON’s ECU Performance Monitoring service regularly analyzes your ECU’s trace data to ensure that potential performance issues are flagged and can be resolved when they arise.
For more information, take a look here.
Including Timing in Requirements Documents
Requirements documents for ECUs focus primarily on functionality but offer little information regarding temporal requirements.
This is proving increasingly problematic as more functions are integrated into a single ECU as the industry moves to zonal architectures.
INCHRON’s Requirements Engineering service heightens awareness for timing and event chains by using common language across shared documentation and processes.
Tackle Complexity in E/E Architectures
Render Complex Systems Manageable:
Understand the causes of interference between different software functions, breaking them down into individual components for examination.
Front-Loaded What-If Analysis:
Uses model-based simulation to determine the impact of software changes, assigning tasks to different cores, varying interrupt priorities, or changes in execution time without building binaries and flashing to the ECU.
Improved Interdisciplinary Collaboration:
Enables software developers, systems engineers, and network architects to separate concerns and understand boundaries. Leads to a smoother integration process and fewer design iterations.
Optimized Team Operation:
Avoid starting expensive task force groups to resolve software issues caused by timing challenges. Lower project costs and improve overall project efficiency.
Competitive Advantage:
Be better prepared to tackle design changes, assess the impact of adding new features, and deliver complex projects to the agreed SoP.
“…we found errors 12 months earlier than usual and were able to understand the root causes and solve them efficiently.”
Thomas Jäger, Bosch, Architect ADAS
Service Process
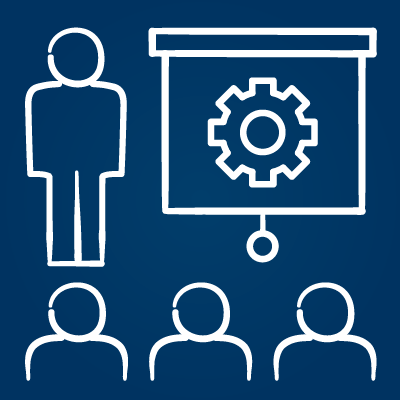
Customer Workshop
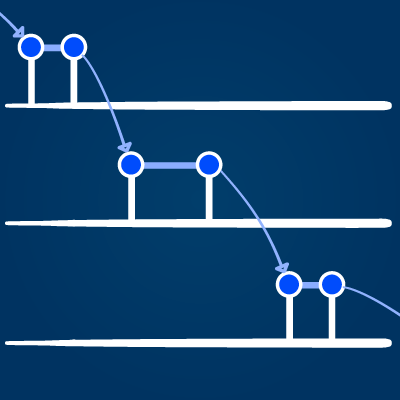
Identify Event Chains
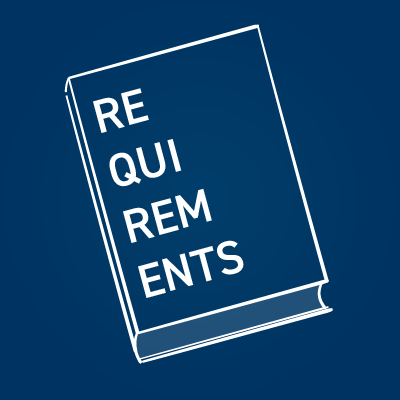
Define
Timing Requirements
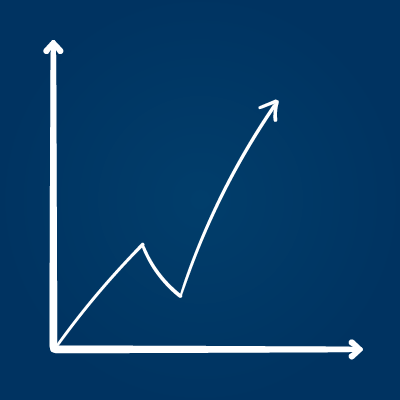
Ongoing Project Management
Working Alongside Your Team
Methodology Alignment:
Clarify tools used for static architecture design, level of abstraction, focus area, and middleware choices.
Event Chain Identification:
Dissect context-adaptive systems to determine event chains. Requires interviews with function owners.
Timing Requirement Specification:
Formal documentation using a machine-readable domain-specific language.
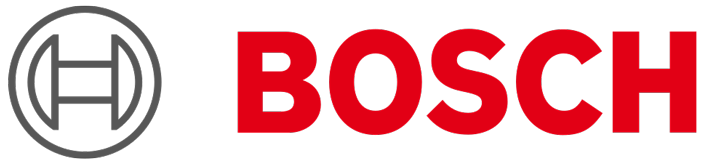
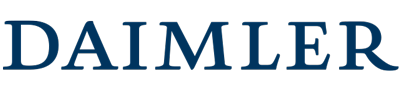
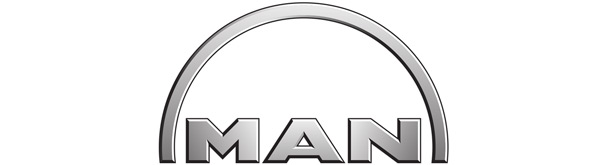
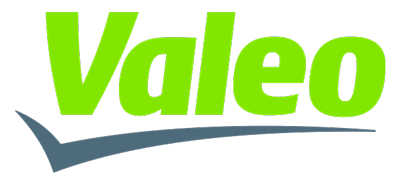
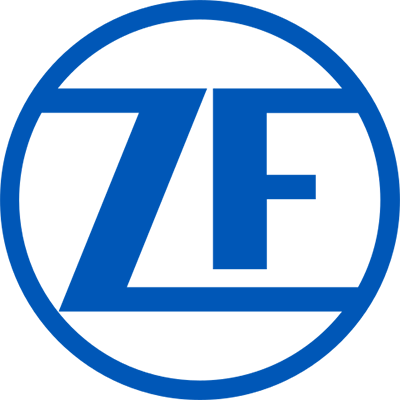
Service Process
Projects kick off with a customer workshop, working alongside all stakeholders to understand the status of the project, the tools being used, and the role and contributions of external suppliers.
From here, the task of identifying event chains across the system begins. Function owners are interviewed to understand the project’s dynamic timing requirements. This leads to the definition of event chains and their timing requirements.
The results of this process are documented for the team. Ongoing support is also provided for the project’s duration to tackle changes that arise in functionality and the impact they have on event chain timing.
“Later project phases were less stressful because frustrating, timing-related sporadic failures did not occur.”
Christian Winkler, MAN Truck & Bus AG, Senior Manager
Frequently Asked Questions (FAQ)
What static architecture formats are supported?
We try to support the file formats used by our customers as far as possible. Common industry formats are supported.
Please get in touch to discuss your needs.
What level of abstraction is supported for the definition of event chains?
Event chains can be defined at the logical, functional, and technical levels. What is most suitable depends on the customer’s project needs.
We are working at a high/low level. Can you still help?
Yes, event chains can be determined at the level of the entire vehicle, component, control unit, and functional level. Most projects require that several levels need to be considered.
What middleware technologies do you support?
AUTOSAR remains a popular choice for ECUs. However, the market continues to change and develop, with a growth in POSIX operating systems and proprietary middleware. INCHRON can support all commonly used middleware and proprietary solutions on request.
My project has already started. Can you still help me?
We’re able to join and support your team at whatever development stage they’ve determined issues related to timing. However, drawing upon INCHRON’s services as early as possible in your project makes the most sense, as this delivers the broadest choice of measures to tackle such issues.
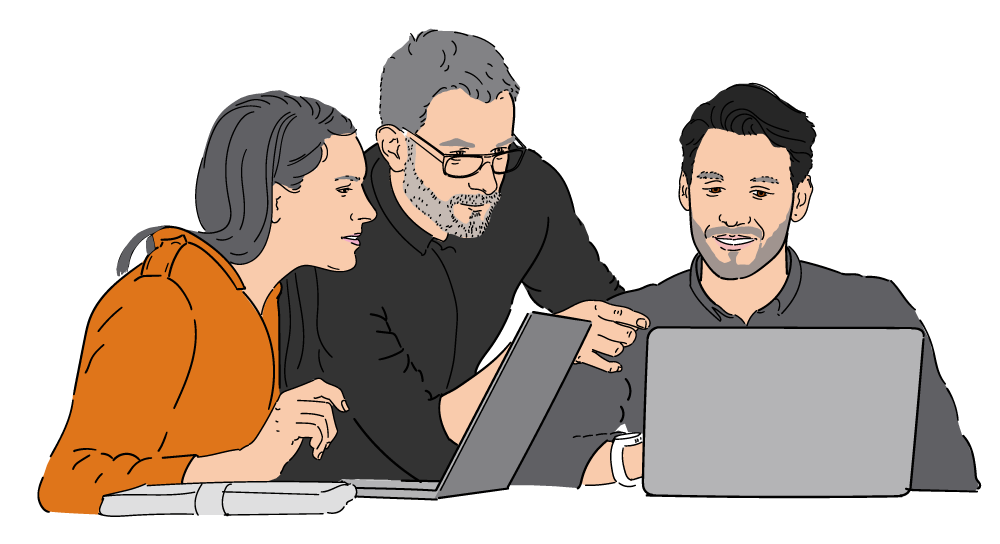
Get in Touch
If you’re looking for support with event chain engineering for your automotive software or ECU development project, use the form below to get in touch.